The secretary of the Army announced an advanced manufacturing policy this week that looks to use technologies like 3D-printing, robotics, artificial intelligence and composite materials to change everything from how soldiers fix equipment in the field, to how much their weapon systems weigh.
As opposed to an armor brigade combat team requesting replacement parts from a warehouse 1,000 miles away, troops could eventually have a 3D-printer churning them out inside the Conex box of a sustainment brigade, putting an Abrams tank back into the fight faster and cheaper.
Army Secretary Ryan D. McCarthy said the initiative he signed will put strategic guidance out to the service and industry partners to indicate that Army leaders will be putting the resources, people and funding into advanced manufacturing technology in future funding plans.
“We’re already doing it in 2021, but we needed to get more aggressive so we could have a comprehensive approach,” McCarthy told Army Times.
The Army has had some success in looking at advanced manufacturing concepts, such as the work done in 3D-printing at Rock Island Arsenal, Illinois, where a Center of Excellence for Advanced and Additive Manufacturing was stood up in May.
“We want to now tie that with all the research and development efforts that we have with Army Futures Command, bring [Army Materiel Command] together," McCarthy said. "Dr. [Bruce D.] Jette, our acquisition executive, puts this policy together, works with industry to have a more comprehensive approach.”
What does advance manufacturing look like?
Additive manufacturing, also known as 3D printing, composite materials and machine learning have already brought a new industrial revolution to private industry, according to Dr. Alexis L. Ross, a deputy assistant Army secretary for strategy and acquisition reform.
“This is a significant step forward in manufacturing and design,” Ross said, recalling one of the times she visited an Army vendor’s facilities where they were developing composite materials.
“An interesting composite material where they were taking silicon and metal and essentially fusing it together,” she said. “And that silicon-metal composite ends up being flexible, light weight, resilient, heat resistant ... it’s got these combinations of great physical properties.”
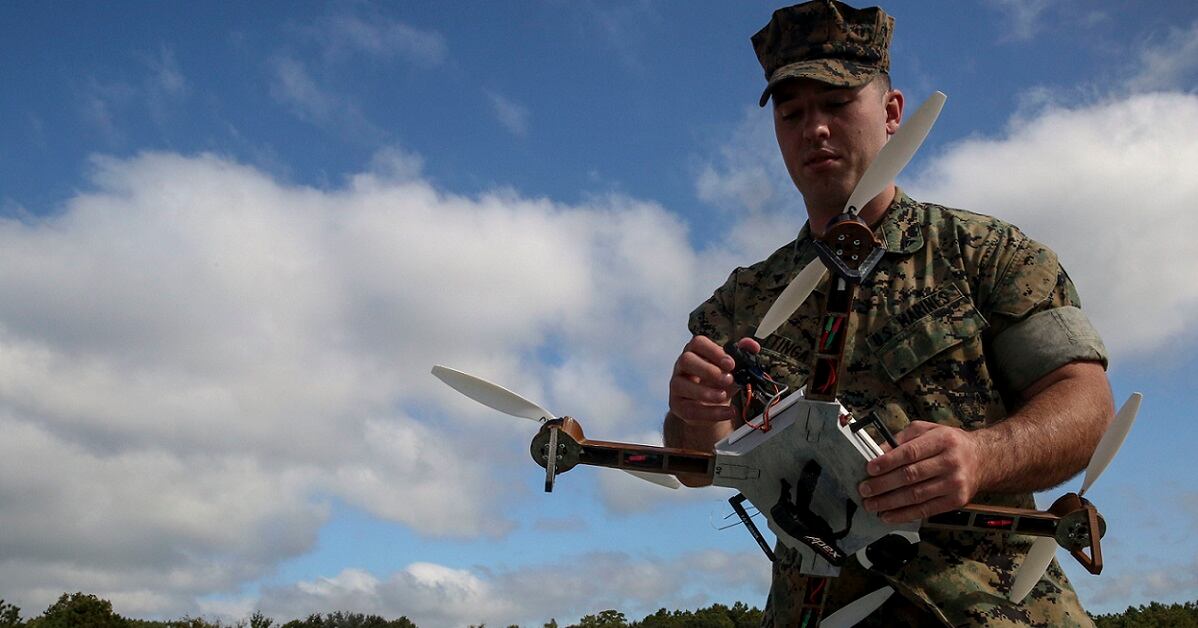
This technology is already available today in the civilian world. A Boeing 737 flying commercially can have parts throughout the airframe that are 3D printed.
Other services, like the Air Force, are already doing this as well.
If private industry and the Air Force can put 3D-printed parts into their aircraft, “why can’t we put that on a ground combat vehicle?" McCarthy said.
So what does it mean for brigade combat teams?
Army leaders hope advanced manufacturing will have two key benefits.
First, it’s expected to reduce the cost of equipment and parts: “If you can produce them much faster, and have them on hand, you can reduce costs because you can be lighter,” McCarthy said.
Second, the technology could significantly enhance the Army’s logistics train, helping its forces fight further away from the U.S. industrial base.
“If you had an expeditionary capability, for example, to print parts, you’d be able to extend the range of a brigade combat team,” McCarthy said. “Their ability to replace parts quickly, doing it within hours, as supposed to weeks. ... There’s an immediate return where you can put it in to tactical formations.”
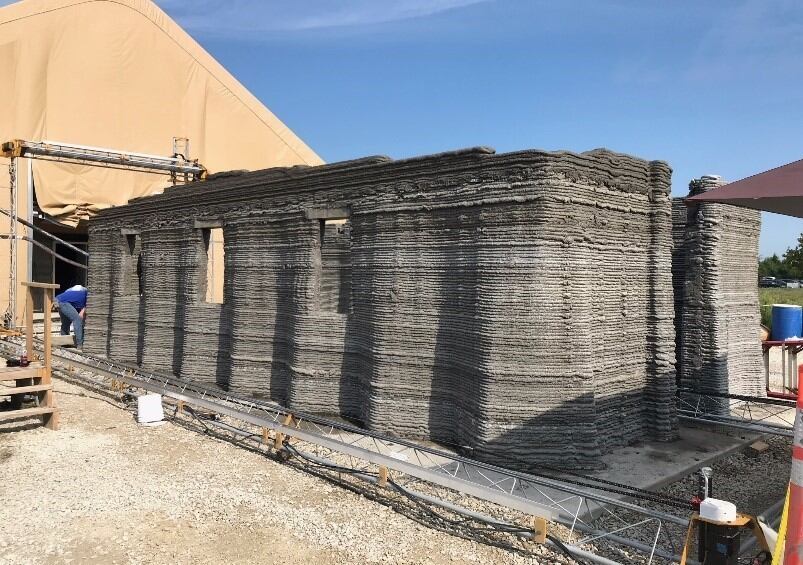
The effort could also help increase operational rates for legacy equipment by shortening the supply chain back to the manufacturer, which may or may not have the right spare parts immediately available.
Those parts, thanks to things like composite materials, could also weigh substantially less.
“A key principle in manufacturing weapons systems is how do you find ways to reduce the weight of the weapon system so it is faster and it can carry more weapons or avionics payloads, because you reduced the weight of parts," McCarthy said.
Moving forward on advanced manufacturing is necessary to keep pace with the United States’ peer adversaries, namely China, according to Ross.
“China has been investing significantly,” she said. “They’re predicted to be the largest user of robotics in production by the year 2025. They just bought 400,000 3D-printers and they’re putting them in every elementary school in the next two years.
“If we don’t start taking action, we will fall behind and we need to catch up," she added.
Kyle Rempfer was an editor and reporter who has covered combat operations, criminal cases, foreign military assistance and training accidents. Before entering journalism, Kyle served in U.S. Air Force Special Tactics and deployed in 2014 to Paktika Province, Afghanistan, and Baghdad, Iraq.