One problem with space is once you’re there you’re in the middle of nowhere. A broken tool or a missing part outside Earth’s atmosphere is a really big deal. Sending replacements is a long and expensive process, not to mention a risky one.
In the “Star Trek” science fiction franchise, a machine on the Starship Enterprise known as the “replicator” offered astronauts a simple solution: create objects on-board, on-demand and out of thin air. Today, recent advances in 3D printing, or additive manufacturing, may be bringing the replicator closer to a reality.
There is just one problem: Before embracing 3D printing for space, scientists want to be sure that 3D-printed materials can function and survive in the harsh space environment over the long haul.
Harris Corporation, along with the International Space Station, is running an experiment to determine just that. The company announced plans Nov. 29 to send a 3D-printed radio frequency (RF) antenna into space to study how such a drastic change in environments will affect its performance.
“The objective is to fly an experiment consisting of 3D-printed materials and analyze the RF properties of those materials in a space environment,” said Dr. Arthur Paolella, senior scientist for Harris Space and Intelligence Systems.
Beyond the convenience of in-space conception, scientists see 3D printing as a promising method for manufacturing RF systems because of its low cost and ability to print complex shapes and conformable systems that traditional manufacturing cannot.
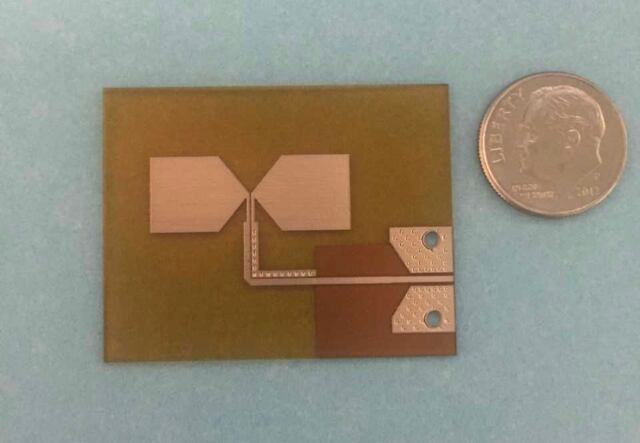
“3D printing provides the freedom to print complex structures more easily,” Dr. Paolella said.
“As far as we know, this will be the first systematic approach to analyzing 3D-printed materials for RF systems in space.”
The project is part of the Materials International Space Station Experiment, a series of experiments mounted on the outside of the International Space Station with the goal of investigating the effects of long-term exposure of materials to the harsh space environment.
There are several key environmental challenges that space operations will present to the 3D-printed materials.
One immediate concern is the extreme temperature variations seen in low-Earth orbit. Because spacecrafts move in and out of sunlight many times per day while orbiting around Earth, temperatures can range from -120 degrees Celsius to +120 degrees Celsius.
Additionally, the RF systems will have to withstand high levels of ultraviolet radiation; highly reactive levels atomic oxygen; and constant impacts from micrometeoroid and other orbital debris.
"The plan is to test the RF system at three points in the program: pre-flight, in-flight and post-flight,” says Paolella.
“We are very optimistic. The circuits developed to this date show good RF performance and have suitability for space applications.”
Harris has partnered on the project with the Israeli-based company Nano Dimension, known for its innovative 3D printers. Using Nano Dimension’s DragonFly 2020 printer, the companies have developed a 3D-printed proof-of-concept RF antenna designed to operate at 5.2 GHz and an RF amplifier with operation up to 6 GHz. The development of the hardware is expected to take one year, according to Paolella.
Funding for the project came from the Harris Innovation Office and the Space Florida Foundation, the aerospace economic development agency of the State of Florida.